Contents
In the realm of computer numercial control (CNC) machining, CNC routers and CNC mills are two of the most commonly used machines. Both are essential for various manufacturing processes, but they serve different purposes and are designed for different applications. Understanding the distinctions between the two can help manufacturers select the right tool for their specific needs.
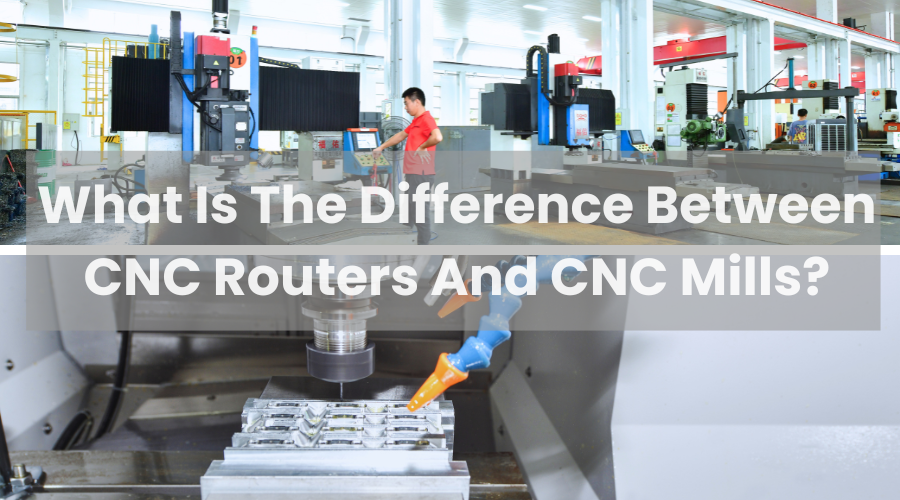
Understanding CNC Technology
Before diving into the specifics of CNC routers and mills, it's essential to grasp the fundamental concept of CNC technology. CNC machines utilize computer software to control tools and machinery, enabling precise, automated operations. This technology is prevalent in various industries, including woodworking, metalworking, plastic fabrication, and aerospace.
CNC Routers: Overview
A CNC router is a computer-controlled cutting machine used primaily for routing (hollowing out) materials such as wood, plastic, foam, and soft metals. These machies are often used for creating intricate designs, signs, furniture components, and decorative pieces.
The CNC Routing Process
1.Design Creation
The process begins with creating a digital design using CAD software. The design can be a 2D sketch or a 3D model, dpending on the project's requirements.
2.Toolparth Generation
Once the design is complete, it is imported into CAM software, which generates the toolpaths. Toolpaths are the paths that the cutting tool will follow to create the desired shapes and features. the CAM software converts these toolpaths into G-code, the language understood by the CNC controller.
3.Material Setup
The material to be cut is secured to the CNC router's bed. This can be done using a vacuum hol-down system, clamps, or double-side tape. Proper material setup is crucial to ensure accurate cuts and avoid movement during machining.
4.Machine Calibration
Before staring the cutting process, the CNC router must be calibrated. This involves setting the zero point (home position) for the X, Y, and Z axes. The zero point acts as the reference for all movements and cuts.
5.Running the CNC Program
With the material secured and the machine calibrated, the CNC router is ready to run the G-code program. The controller reads the G-code and directs the spindle and drive system to move along the specified toolpaths.
6.Cutting and Machining
As the spindle moves along the toolpaths, it rotates the cutting tool at high speeds to remove material and create the desired shapes. The movements are precise, allowing for intricate designs and detailed work. The cutting speed, feed rate, and depth of cut are all controlled by the G-code and can be adjusted based on the material and tool being used.
7.Finishing
After the cutting process is complete, the finished part is removed from the bed. Additional finishing operations, such as sanding, polishing, or painting, may be required depending on the project's requirements.
Applications of CNC Routers
- Woodworking (cabinetry, furniture)
- Sign making
- Model making
- Prototyping
- Archtetural detailing
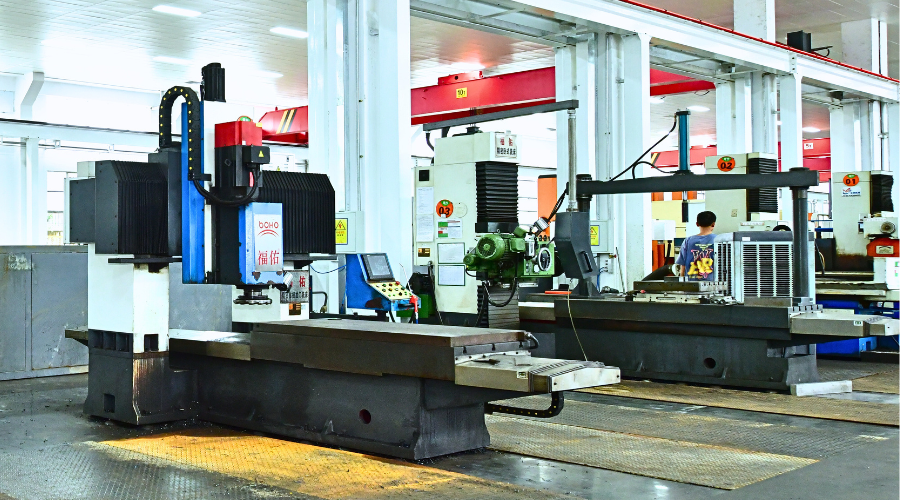
CNC Mills: Overview
A CNC mill, on the other hand, is designed for more rigorous machining operations, often used to create precise components from hard materials such as metals, plastics, and composites. CNC mills are typically employed in industrial manufacturing processes requiring high precision and durability.
The CNC Milling Process
1.Design Creation
The process starts with creating a digital design using CAD software. This design can be a 2D drawing or a 3D model, depending on the complexity of the part.
2.Toolpath Generation
Once the design is complete, it is imported into CAM software. The CAM software generates the toolparths, which are the parths that the cutting tool will follow to create the desired shapes and features. These toolpaths are then converted into G-code.
3.Material Setup
The material to be machined is secured to the machine table using clamps, vises, or fixtures. Proper material setup is crucial to ensure stability and accuracy during the machining process.
4.Machine Calibration
Before starting the machining process, the CNC mill must be calibrated. This involves setting the zero points (home positions) for the X, Y, and Z axes. The zero points serve as references for all subsequent movements and cuts.
5.Running the CNC Program
With the material secured and the machine calibrated, the CNC mill is ready to run the G-code program. The controller reads the G-code and directs the spindle and drive system to move along the specified toolpaths.
6.Cutting and Machining
As the spindle moves along the toolpaths, it rorates the cutting tool at precise speeds to remove material and create the desired shapes. THe movements are controlled with high precision, allowing for intrcate detailing and tight tolerances. The cutting speed, feed rate, and depth of cut are all controlled by the G-code and can be adjusted based on the material and tool being used.
7.Tool Changes
If the part requries multiple operations with different tools (e.g., drilling, milling, reaming), the CNC mill can automatically change tools using the ATC. This feature enhances efficiency and reduces downtime.
8.Finishing
After the machining process is complete, the finished part is removed from the table. Additional finishing operations, such as deburring, sanding, or polishing, may be required depending on the project's requirements.
Applications of CNC Mills
- Aerospace components
- Automotive parts
- Medical devices
- High-precision tooling
- Prototyping and production of complex parts
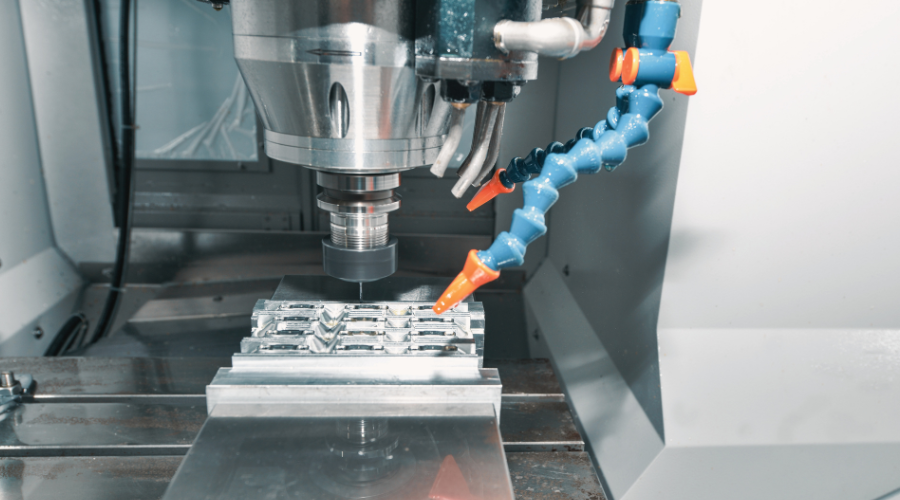
Key Differences Between CNC Routers and CNC Mills
1.Material Types
CNC Routers: Best for softer mateirals like wood, plastics, and foam.
CNC Mills: Designed for harder materials, including metals and composites.
2.Precision and Tolerance
CNC Routers: Generally less precise than mills; suitable for applications where ultra-tight tolerances are not critical.
CNC Mills: High precision and tighter tolerances, making them ideal for engineering and aerospace applications.
3.Design and Construction
CNC Routers: Often feature a gantry-style design with a flat bed.
CNC Mills: Typically have a rigid, vertical structure that supports heavy machining.
4.Tooling and Operation
CNC Router: Utilize high-speed spindle rotation with various bits for different cuts.
CNC Mills: Use a variety of tools for different operations, requiring tool changes for complex projects.
5.Cost and Complexity
CNC Routers: Generally more affordable and user-friendly for beginners.
CNC Mills: Usually more expensive and complex, suitable for skilled operators.
Choosing Between CNC Routers and CNC Mills
Chhosing deciding between a CNC router and a CNC mill, consider the following factors:
- Material Requirements: Identify the materials you will be working with. If your projects primary involve soft materials, a CNC router is likely more suitable. For hard materials or precise engineering tasks, a CNC mill is the better choice.
- Project Complexity: For intricate designs requiring detailed work, CNC mills provide the necessary precision. For larger, less complex projects, routers are often adequate.
- Budget: Evaluate your budget constraints. CNC routers tend to be less expensive, making them more accessible for small businesses or hobbyists.
- Skill Level: Consider the skill level of the operators. CNC routers may be easier for beginners to learn, wihle CNC mills may require more advanced knowledge.
Conclusion
Both CNC routers and CNC mills are invaluable tools in the manufacturing, each serving distinct purposes and applications. Understanding their differences in materials, precision, design, tooling, and cost will help you make an informed decision based on your specific needs. Wheter you require the versatility of a CNC router for woodworking or the precision of a CNC mill for metalworking, selecting the right machine is essential for achieving your project goals.