Plastic welding is a process that joins two or more plastic parts by melting the surfaces to be joined and allowing them to cool, resulting in a solid bond. This method is widely used in various industries due to its versatility and precision.
From automotive to medical and from consumer electronics to aerospace, plastic welding plays a crucial role in manufacturing and assembly processes. Its ability to create strong, sealed, and leak-proof joints makes it indispensable for many applications.
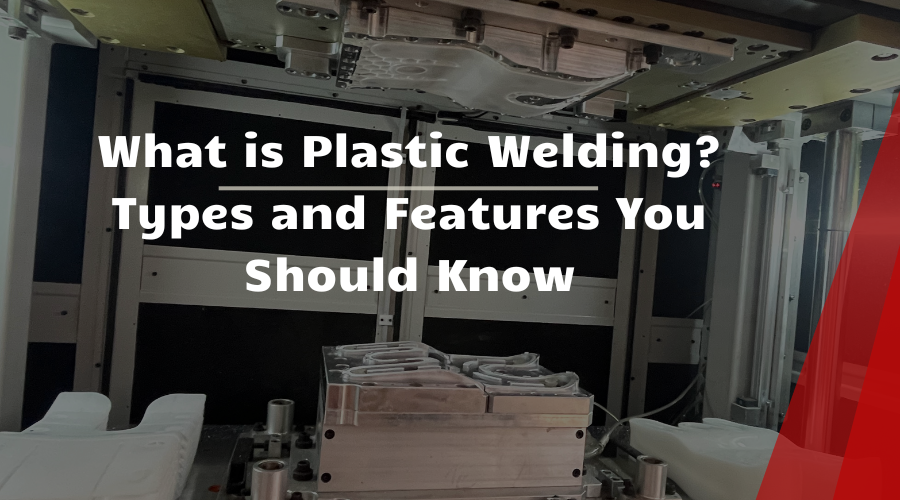
What is Plastic Welding
Plastic welding is a thermo-joining technique that involves the application of heat and pressure to the plastic material, causing the materials to melt and fuse together, thus creating a permanent bond. This process is distinct from traditional metal welding, which relies on the melting of the base material itself.
In plastic welding, the heat is often applied externally, and the materials are joined through the use of various techniques that facilitate the melting and fusing process.
Common plastic materials suitable for welding
Common materials that are suitable for plastic welding include polyethylene(PE), polypropylene(PP), polyvinyl chloride(PVC), and polycarbonate(PC). The selection of the welding technique often depends on the type of plastic being joined.
- Polyethylene (PE): Known for its flexibility and chemical resistance, PE is commonly used in applications such as piping and geomembranes. It is thermoplastic, making it a good candidate for welding.
- Polypropylene (PP): PP is appreciated for its resistance to fatigue and its ability to withstand high temperatures. It is often used in the automotive and packaging industries and is also amenable to welding processes.
- Polyvinyl Chloride (PVC): PVC is a versatile material used in a wide range of applications, from pipes to medical equipment. It can be welded using techniques such as hot air or hot gas welding, which are effective for PVC’s rigid and semi-rigid forms.
- Polycarbonate (PC): Due to its exceptional impact resistance and clarity, PC is used in the manufacturer of eyeglass lenses, compact discs, and protective gear. It can be welded, but due to its high melting point, specialized techniques such as ultrasonic or infrared welding are often required.
Types of Plastic Welding Techniques
Plastic welding is a versatile process that can be tailored to variety of applications and materials. Different techniques have been developed to cater to the diverse needs of the plastic fabrication industry.
- Hot Gas Plastic Welding
- Explanation of the process: Hot gas welding involves the use of a heated gas, such as a propane torch, to melt the plastic surfaces. The parts are then pressed together and cooled to form a bond.
- Advantages and limitations: This method is simple and cost-effective but may not be suitable for all types of plastics and can result in a less precise bond compared to other methods.
- Typical applications: Commonly used for welding pipes, fittings, and large plastic structures.
- Spin Welding (Friction Welding)
- How the process is performed: Spin welding uses friction to generate heat by spinning one plastic part against another under pressure. Once the plastic reaches its melting point, the spinning stops, and the parts are held together to cool and bond.
- Benefits anddrawbacks: Spin welding is precise and produces strong bonds but requires specific equipment and is limited to thermoplastics.
- Suitable plastic types and industries where it’s commonly used: Often used with thermoplastics like polyethylene and polypropylene, it’s prevalent in the medical and pharmaceutical industries.
- Ultrasonic Plastic Welding
- Principles behind ultrasonic welding:Ultrasonic welding uses high-frequency vibrations to generate frictional heat at the joint interface, melting the plastic and creating a solid-state bond.
- Equipment required: An ultrasonic welder with a converter, booster, and horn is necessary for this process.
- Industries and products that benefit from this method: Ultrasonic welding is ideal for medical devices, disposable products, and electronics where precision and cleanliness are paramount.
- Infrared Plastic Welding
- Description of the infrared welding process: Infrared welding uses infrared radiation to heat the plastic, which is then pressed together to form a bond.
- Pros and Cons:This method offers a non-contact approach, reducing the risk of contamination, but may require more complex equipment and setup.
- Specific use cases and material compatibility:Infrared welding is well-suited for heat-sensitive plastics and is used in the automotive and packaging industries.
Each plastic welding technique offers unique advantages and is designed to meet specific industrial needs. By understanding the principles and applications of plastic welding, professionals can select the most appropriate method to ensure a high-quality, reliable, and efficient plastic welding process.
Key Features of Effective Plastic Welding
When it comes to plastic welding, several key features determine the effectiveness and suitability of the process for a given application. These features ensure the quality and longevity of the weld and contribute to the sustainability and economic viability of the welding operation.
- Strength and Durability of Welds: Effective plastic welding must produce strong and durable bonds that can withstand the stresses and strains of the application environment.
- Precision and Control: The ability to control the welding process precisely is critical for achieving consistent and high-quality results.
- Different Plastic Types:A good plastic welding process should be adaptable to a range of plastic materials to accommodate various applications.
- Environmental and Cost-Efficiency: The welding process should be environmentally friendly, minimize waste and emission, and be cost-effective, providing value for the investment.
Safety Precaution in Plastic Welding
While plastic welding offers numerous advantages in terms of versatility and efficiency, it is imperative to prioritize safety at every step of the process. Adhering to strict safety protocols is essential to protect workers, ensure the quality of the weld, and maintain a productive and secure work environment.
- Personal Protective Equipment (PPE)
Wear appropriate PPE, including heat-resistant gloves, safety glasses, and protective clothing to prevent burns and injuries. The right PPR protects the welder not only from the intense heat generated during the process but also from any flying debris or hazardous materials that may be present.
- Proper Ventilation and Fume Control
Ensure proper ventilation to avoid the buildup of fumes and maintain a safe working environment. Many plastic materials, when heated, can release harmful fumes if inhaled in large quantities. Ventilation systems should be designed to effectively remove these fumes, thereby reducing the risk of respiratory issues and other health problems.
- Handling of Equipment and Materials
Follow the manufacturer’s guidelines for operating the welding equipment and handling the materials to prevent accidents and ensure the quality of the weld. Misuse of equipment or improper handling of materials can lead to accidents, compromised weld quality, and even damage to the equipment itself.
Conclusion
In conclusion, plastic welding is an indispensable technique in modern manufacturing, offering a range of benefits, from precision and versatility to environmental and economic advantages.
By understanding the various types of plastic welding techniques, their key features, and the importance of safety precautions, professionals can harness this powerful process to create high-quality, durable, and reliable products across a multitude of industries. HordRT is such a company that provides these professional services.
HordRT offers advanced plastic injection molding services .