Contents
CNC machining is known for its precision and versatility, but two critical aspects that can make or break the success of any machining project are tolerances and surface finish. These factors determine the functional and aesthetic quality of machined components. Understanding how to achieve desired tolerances and surface finishes is important for manufacturers looking to meet client specifications, maintain cost-efficiency, and ensure the reliability of machined parts.
In this article, we will explore:
- The concept of tolerances and their importance in CNC machining
- How surface finish affects part performance and quality
- The relationship between tolerances and surface finish
- Techniques and strategies to achieve tight tolerances and optimal surface finishes
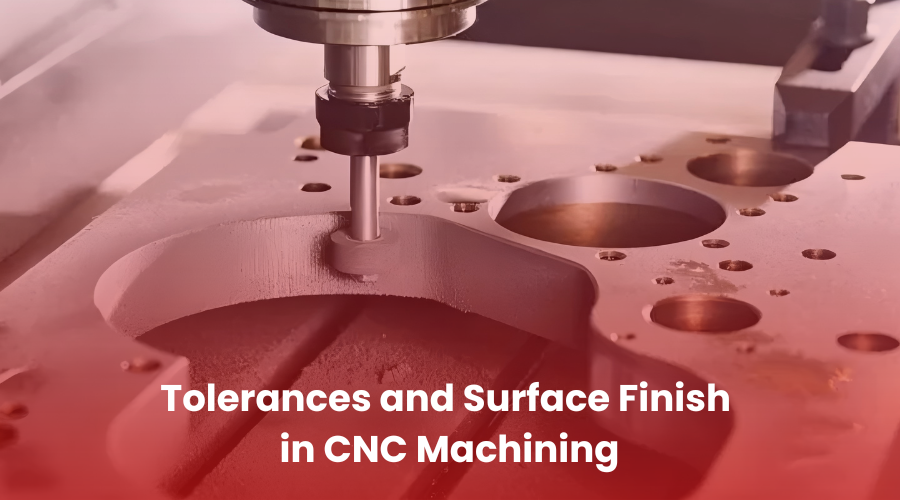
1. Understanding Tolerances in CNC Machining
1.1 What are Tolerances?
In CNC machining, tolerances refer to the allowable deviation from the specified dimensions of a part. No machining process is perfect, and even the most precise equipment will exhibit some degree of variation. Tolerances define the range within which this variation is acceptable. These tolerances are usually denoted in engineering drawings as "+/-" values around a nominal dimension.
Tolerances can range from very loose (±0.1mm) to extremely tight (±0.001mm), depending on the application. Precision machining typically involves much tighter tolerances to ensure that components fit together correctly and function as intended in their final assembly.
1.2 Types of Tolerances
- Linear Tolerances: These specify the allowable variation in linear dimension, such as the length, width, or height of apart. For example, a part specified as 100mm ±0.02mm can be anywhere between 99.98mm and 100.02mm.
- Geometric Tolerances: These refer to the allowable variation in the shape or form of a part, including flatness, circularity, cylindricity, and perpendicularity.
- Angular Tolerances: These are used when specifying the permissible variation in an angle. They are crucial in components that require precise angles for assembly or functionality.
1.3 Importance of Tolerances
Tolerance ensures that parts manufactured in different locations or batches can fit together seamlessly in assemblies. In industries like aerospace, automotive, and medical device manufacturing, tight tolerances are essential for ensuring safety, reliability, and performance.
1.4 Poor Tolerance Control Can Result in:
- Assembly Issues: Parts may not fit together correctly.
- Performance Degradation: Improperly toleranced parts can lead to poor performance or even failure under load or stress.
- Increased Costs: Tight tolerances require precision machining, which often means longer machining times and higher costs.
2. Surface Finish in CNC Machining
2.1 What is Surface Finish
Surface finish refers to the texture or smoothness of a machined surface. It is often described in terms of surface roughness, measured in micrometers (µm). The surface finish is a result of various factors, including tool geometry, feed rate, cutting speed, and the type of material being machined.
2.2 Types of Surface Finishes
Surface finishes can range from tough to mirror-like smoothness, depending on the application:
- Rough Machining: This results in a relatively coarse surface finish, often with visible tool marks. Rough machining is typically used when surface aesthetics are less important.
- Semi-Finishing: This process refines the surface finish, reducing tool marks and achieving better dimensional accuracy.
- Fine Finishing: This produces a very smooth surface, often used for aesthetic or high-performance
2.3 Measuring Surface Roughness
Surface roughness is commonly measured using instruments such as a profilometer or a surface roughness tester. The key parameters include:
- Ra (Arithmetic Average Roughness): The average f surface height deviations from the mean line.
- Rz (Average Maximum Height): The average distance between the highest peak and the lowest valley in a surface texture profile.
A low Ra value indicates a smoother surface, while a high Ra value indicates a rougher surface.
2.4 Importance of Surface
Surface finish is critical for the performance and functionality of parts. A poor surface finish can lead to:
- Increased Friction: Rough surface may cause increased friction between moving parts, leading to wear and reduced efficiency.
- Fatigue Cracks: Poor surface finish can create stress concentrators, which may lead to fatigue cracking under cyclic loading.
- Aesthetic Defects: For parts that are visible in the final assembly, surface finish is essential for meeting aesthetic requirements.
In applications like aerospace or medical devices, the surface finish can also affect how the part interacts with other materials, such as fluids or biological tissues, making it a crucial parameter for functional performance.

3. The Relationship Between Tolerances and Surface Finish
Tolerances and surface finish are closely related in CNC machining. Achieving tight tolerances often requires fine control over surface finish, and vice versa. For instance, to achieve very tight tolerances, a part may need to undergo multiple finishing operations to ensure both dimensional accuracy and surface smoothness.
However, it's important to note that tighter tolerances and finer surface finishes often increase machining costs. More precise machining requires:
- Slower Feed Rates: Reducing the speed at which the tool moves can improve surface finish but also increase cycle time.
- Advanced Tooling: Specialized cutting tools may be required to achieve both tight tolerances and fine finishes.
- Additional Processes: Secondary processes, such as polishing or grinding, may be necessary to refine the surface after the initial machining operation.
Striking the right balance between tolerance, surface finish, and cost is essential for manufacturers. Over-specifying tolerances or surface finishes can lead to unnecessary machining complexity and cost, while under-specifying can compromise part performance or assembly fit.
4. Achieving Tight Tolerances in CNC Machining
Machine Calibration and Maintenance
Achieving tight tolerances requires highly calibrated and well-maintained CNC machines. Regular machine calibration ensures that axis positioning and tool movements remain accurate over time.
Tooling Selection
Selecting the right cutting tools is crucial. Precision tools with minimal wear can help maintain consistent tolerances across multiple parts. Carbide tools, for example, offer higher durability and precision compared to standard HSS (high-speed steel) tools.
Thermal Compensation
Thermal expansion can affect both the workpiece and the CNC machine itself, leading to dimensional changes during machining. Advanced CNC systems often include thermal compensation features, which adjust for temperature fluctuations to maintain tight tolerances.
Tool Wear Monitoring
Tool wear can cause deviation from desired tolerances. CNC machines equipped with in-process monitoring can detect tool wear early, prompting tool changes before tolerances issues arise.
5. Achieving Optimal Surface Finish
5.1 Cutting Parameters
The cutting parameters — such as speed, feed rate, and depth of cut — play a crucial role in determining surface finish:
- Cutting Speed: Higher cutting speeds often produce smoother finishes, but excessive speeds can lead to tool wear.
- Feed Rate: Lower feed rates generally result in better surface finishes, but they also increase machining time.
- Depth of Cut: Shallower cuts are more likely to produce fine finishes but may require multiple passes.
5.2 Tool Geometry
The geometry of the cutting tool, including the rake angle, clearance angle, and nose radius, significantly impacts the surface finish. Tools with larger nose radii tend to produce smoother finishes by distributing the cutting forces over a larger area.
5.3 Machining Environment
Coolants and lubricants can help improve surface finish by reducing friction and dissipating heat during cutting. Proper coolant application reduces tool wear, minimizes chip adhesion, and enhances surface smoothness.
5.4 Secondary Finishing Operations
In some cases, secondary operations such as grinding, polishing, or lapping may be required to achieve the desired surface finish. These processes can smooth out any imperfections left after machining and bring the surface roughness within specified limits.
Conclusion
In CNC machining, tolerances and surface finish are two critical factors that determine the functionality, performance, and quality of a machined part. While tolerances ensure that parts meet dimensional specifications, surface finish affects how parts perform under different operational conditions, including friction, wear, and stress.
Achieving both tight tolerances and optimal surface finishes requires careful planning, the right choice of tools, well-calibrated machines, and the use of appropriate cutting parameters. While tighter tolerances and finer finishes often result in higher costs, they are indispensable in industries where precision and performance are paramount, such as aerospace, medical devices, and high-end manufacturing.
Understanding the interplay between tolerances, surface finish, and cost can help manufacturers strike the perfect balance, ensuring that parts not only meet functional requirements but also remain cost-effective to produce.
At HordRT, a customized manufacturer specializing in precision machining, we prioritize delivering parts with exceptional accuracy and high-quality finishes. Whether you require tight tolerances, fine surface finishes, or both, our advanced CNC machining processes and experienced team ensure that your parts meet the highest standards. Contact us today to learn how we can support your next project with precision excellence.