As we all know, material selection is a critical factor in determining the quality and performance of the final product in the process of injection molding. Among the myriad of materials available, nylon stands out as a versatile and precious option. Known for its strength, durability, and flexibility, nylon has become a popular choice for manufacturers across various industries. In this article, we will delve into the properties, applications, types, and benefits of using nylon in plastic injection molding.
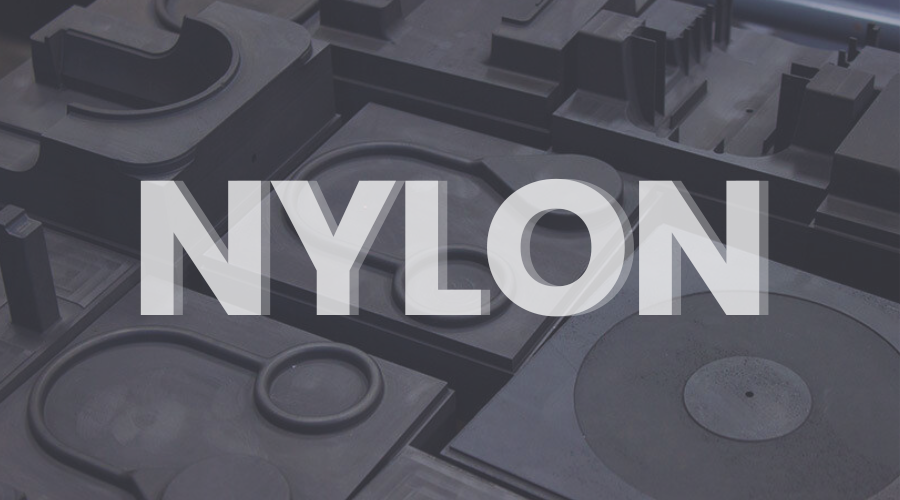
What is Nylon?
Nylon is a synthetic polymer, specifically a type of polyamide, known for its strength, durability, and versatility. It was first developed in the 1930s and has since been used in a wide range of applications, including textiles, automotive parts, and industrial products. Nylon is resistant to abrasion, chemicals, and heat, making it a popular choice for items like clothing, ropes, and engineering plastics. There are several types of nylon, with Nylon 6 and Nylon 6/6 being the most common.
Key Properties of Nylon
- High Strength and Durability: Nylon is renowned for its high tensile strength, making it ideal for applications that require robust and durable components. It can withstand significant mechanical stress and wear, ensuring longevity and reliability in demanding environments.
- Excellent Chemical Resistance: Nylon exhibits strong resistance to a wide range of chemicals, including oils, solvents, and fuels. This makes it suitable for use in automotive, industrial, and consumer goods where exposure to harsh substances is common.
- Thermal Stability: Nylon can maintain its properties across a broad temperature range. It performs well in both high and low0temperature environments, making it a versatile choice for applications that experience extreme temperature variations.
- Low Frication Coefficient: The low friction coefficient of nlon makes it an excellent material for components that require smooth movement and reduced wear, such as gears, bearings, and bushings.
- Good Electrical Insulation: Nylon is an effective electrical insulator, which is beneficial for applications in the electronics inudstry where electrical conductivity needs to be minimized.
- Verdatility in Processing: Nylon is highly adaptable to various processing techniques, including plastic injection molding. Its meld flow properties and ease of molding make it suitable for producing complex shapes and intricate designs.
Application of Nylon in Plastic Injection Molding
The versatility of nylon makes it a go-to material for a wide range of industries. Some common applications include:
- Automotive Industry: Nylon is used in the production of automotive parts such as engine covers, intake manifolds, radiators and tanks due to its high strength, thermal stability, and chemical tesistance.
- Consumer Goods: Household items like toothbrushes, kitchen utensils, and sports equipment often utilize nylon for its durability and aesthetic appeal.
- Electrical and Electronis: Nylon is found in connextors, switches, and housings, where its electrical insulation properties and mechanical strength are advantageous.
- Industrical Applications: Gears, bearing, and conveyor belts made from nylon are widely used in industrial machinery due to their low frication and high wear resistance.
- Medical Devices: Nylon's bio-compatibility and ease of sterilization make it suitable for various medical applications, including surgical instruments and implantable devices.
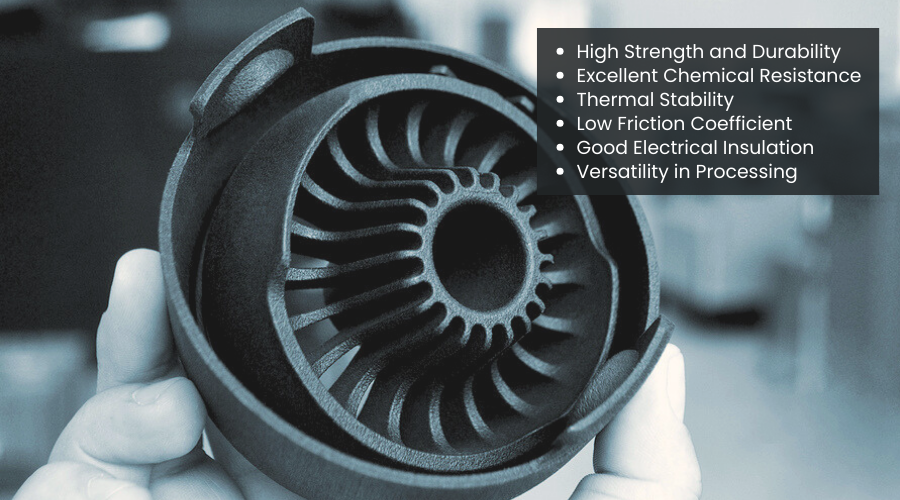
Types of Nylon
The most common types of nylon used in plastic injection molding include nylon 6, nylon 6/6, and several specialized variants. Understanding these types can help manufacturers select the best material for their specific needs.
Nylon 6 (Polycaprolactam)
Properties:
- Molecular Structure: Nylon 6 is a single type of monomer, caprolactam, polymerized to form a long chain.
- Mechanical Strength: It offers good tensile strength and toughness.
- Thermal Stability: It has a melting point of around 220℃.
- Impact Resistance: Excellent impact resistance, even at low temperatures.
- Moisture Absorption: Trends to absorb more moisture compared to nylon 6/6, which can affect its dimensional stability.
Nylon 6/6 (Polyhexamethylene Adipamide)
Properties:
- Molecular Structure: Formed by the condensation of hexamethylenediamine and adipic acid, resulting in a polymer with a repeating unit of six carbon atoms.
- Mechanical Strength: Higher tensile strength and modulus compared to nylon 6.
- Thermal Stability: Higher melting point of around 260℃, making it suitable for high-temperature applications.
- Wear Resistance: Superior wear resistance and lower friction, making it ideal for applications with moving parts.
- Moisture Absorption: less moisture absorption than nylon 6, leading to better dimensional stability.
Nylon 11 (Polyamide 11)
Properties:
- Bio-Based: Derived from castor oil, making it more enviromentally friendly.
- Flexibility: More flexible and less dense than nylon 6 and nylon 6/6.
- Chemical Resistance: Excellent resistance to chemicals, oils, and fules.
- Thermal Properties: Moderate thermal resistance with a melting point of around 190℃.
Nylon 12 (Polyamide 12)
Properties:
- Low Moisture Absorption: Very low moisture absorption, providing excellent dimensional stability.
- Flexibility: Highly flexible, making it suitable for dynamic applications.
- Chemical Resistance: Outstanding resistance to oils, fuels, and other chemicals.
- Thermal Properties: Lower melting point around 180 around 180℃ compared to nylon 6 and nylon 6/6.
Nylon 46 (Polyamide 46)
Properties:
- High Heat Resistance: Exceptional thermal resistance with a melting point around 295℃.
- Mechanical Strength: Superior mechanical strength and stiffness.
- Wear Resistance: Excellent wear and fatigue resistance.
Glass-Filled Nylon
Properties:
- Reinforcement: Contains glass fibers, which significantly enhance its mechanical properties.
- Strength and Stiffness: Increased tensile strength and rigidity.
- Thermal Stability: Improved heat resistance compared to unfilled nylon.
Benefits of Using Nylon in Plastic Injection Molding
- Cost-Effectiveness: Nylon is relatively affordable compared to other high-performance polymers, providing a cost-effective solution without compromising on quality.
- Design Flexibility: The ease of processing nylon through injection molding allows for the creation of complex and precise designs, enabling manufacturers to produce intricate components efficiently.
- Enhanced Performance: The combination of mechanical strength, chemical resistance, and thermal stability ensures that nylon components perform reliably in challenging conditions, extending the lifespan of the final products.
- Sustainability: Advances in nylon production have led to the development of eco-friendly variants, including bio-based and recycled nylons, contributing to sustainable manufacturing practices.
Advancements in Nylon Technology
The continuous development of nylon technology has led to the introduction of enhanced variants, further broadening its applications and benefits. Some of these advancements include:
- Glass-Filled Nylon: By incorporating glass fibers into the nylon matrix, the resulting composite material exhibits significantly improved mechanical properties, such as increased stiffness and strength. This makes glass-filled nylon an excellent choice for structural components and parts subjected to high stress.
- Heat-Stabilized Nylon: For applications requiring prolonged exposure to high temperatures, heat-stabilized nylon offers improved thermal resistance. This variant maintains its mechanical properties even at elevated temperatures, making it suitable for automotive and industrial applications.
- Lubricated Nylon: Self-lubricating nylon variants contain internal lubricants that reduce friction and wear. These materials are ideal for applications where moving parts are involved, such as bearings, gears, and sliding mechanisms.
- Conductive Nylon: By adding conductive fillers, nylon can be made electrically conductive. This is beneficial for applications where static electricity dissipation or electromagnetic interference (EMI) shielding is required, such as in electronic enclosures and connectors.
Challenges and Considerations
while nylon offers numerous advantages, it is essential to consider certain factors to ensure optimal performance:
- Moisture Absorption: Nylon is hygroscopic, meaning it absorbs moisture from the environment. This can affect its mechanical properties and dimensional stability. Proper drying and conditioning processes are necessary before molding to minimize these effects.
- Molding Conditions: Precise control of processing parameters, such as temperature, pressure, and cooling rate, is crucial to achieve the desired quality and performance of nylon components. manufacturers must optimize their molding processes to avoid defects such as warping, shrinkage, and voids.
- Compatibility with Additives: The addition of fillers, reinforcements, and other additives can enhance nylon's properties but may also affect its processability. It is important to ensure compatibility between the base resin and additives to achieve the desired performance without compromising manufacturability.
Conclusion
In summary, nylon has firmly established itself as a premier material for plastic injection molding due to its remarkable properties and versatility. Its high tensile strength, excellent chemical resistance, thermal stability, low friction coefficient, and good electrical insulation make it an ideal choice across various industries. From automotive and consumer goods to electrical, industrial, and medical applications, nylon's adaptability and performance are unmatched. With advancements in nylon technology, such as glass-filled, heat-stabilized, lubricated, and innovative solutions for complex and demanding environments. However, understanding leveraging nylon's full potential. As the industry moves towards more sustainable practices, the development of eco-friendly nylon variants further solidifies its role in the future of plastic injection molding.