Contents
High-Density Polyethylene (HDPE) is a versatile thermoplastic known for its durability, strength, and resistance to various chemicals. These qualities make it a preferred material for injection molding across a wide range of industries, from packaging to automotive components. This article explores the intricates of HDPE injection molding, highlighting its processes, benefits, drawbacks, and diverse applications.
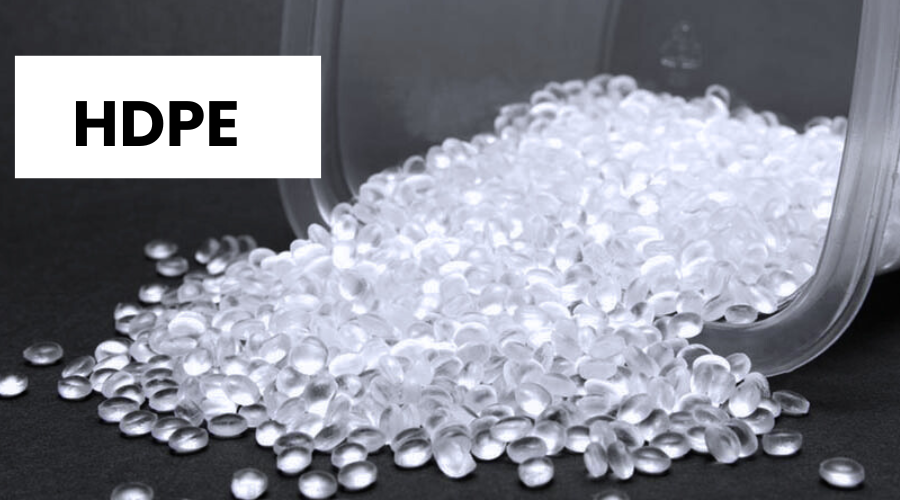
HDPE Injection Molding Process
HDPE injection molding follows a systematic process to create precise and durable parts:
1. Material Preparation: HDPE pellets are fed into a hopper and heated to their melting point in the injection molding machine's barrel.
2. Injection: The molten HDPE is injected into a mold cavity under high pressure using a reciprocating screw mechanism or a plunger.
3. Cooling: Once injected, the mold cools rapidly, solidifying the HDPE into the desired shape.
4. Ejection: After cooling, the mold opens, and the part is ejected, and ready for further processing or use.
Advantages of HDPE Injection Molding
HDPE is widely favored in various industries due to its remarkable properties and advantages. Here are some of the key advantages of HDPE:
- Durability and Strength
- High Tensile Strength: HDPE has excellent tensile strength, allowing it to withstand heavy loads and stresses without breaking or deforming.
- Impact Resistance: It exhibits superior resistance to impacts and physical abuse, making it ideal for applications requiring toughness and resilience.
- Chemical Resistance
- Corrosion Resistance: HDPE is highly resistant to a broad range of chemicals, including acids, bases, and solvents, which makes it suitable for containers and piping systems that carry corrosive substances.
- Non-Reactive: Its inert nature ensures that it does not react with the contents it holds, making it a safe choice for food and beverage packaging.
- Water Resistance
- Low Moisture Absorption: HDPE’s low water absorption rate makes it an excellent material for applications exposed to moisture, such as pipping, containers, and outdoor furniture.
- Waterproof Properties: It remains unaffected by water, preventing degradation and maintaining its structural integrity over time.
- Lightweight
- Ease of Handling: HDPE is lightweight, which simplifies transportation, installation, and handling compared to other materials like metals.
- Reduced Costs: The light weight contributes to lower shipping and handling costs, making it an economical choice for manufacturers and consumers.
- Flexibility and Versatility
- Moldability: HDPE can be easily molded into complex shapes and designs, offering flexibility in manufacturing various products with precise dimensions and intricate features.
- Wide Range of Applications: Its versatility allows it to be used in diverse industries, including packaging, construction, automotive, and medical sectors.
- Cost-Effectiveness
- Lower Material Cost:HDPE is generally less expensive than many other thermoplastics and metals, providing a cost-effective solution for large-scale production.
- Efficient Processing: Its ease of processing and rapid production cycle reduce manufacturing time and costs, increasing overall efficiency.
- Environmental Benefits
- Recyclability: HDPE is fully recyclable, and recycled HDPE can be used to produce new product, reducing the environmental impact and promoting sustainable practices.
- Reduced Waste: Its durability and long lifespan contribute to reduced waste and lower replacement costs over time.
Disadvantages of HDPE
- Susceptibility to Stress Cracking
- Environmental Stress Cracking: HDPE can be prone to stress cracking under certain conditions, especially when exposed to stress and environmental factors over time. This can compromise the integrity of the material in demanding applications.
- Limited High-Temperature Performance
- Heat Sensitivity: HDPE has a relatively low melting point (around 130-137°C or 266-279°F), making it unsuitable for applications involving high temperatures. Prolonged exposure to high temperatures can cause the material to soften, deform, or degrade.
- Flammability: Although HDPE has good resistance to some chemicals, it is flammable and can ignite if exposed to open flames or extreme heat.
- Poor UV Resistance
- Sunlight Degradation: Standard HDPE can degrade when exposed to ultraviolet (UV) light over extended periods. This can lead to brittleness, cracking, and loss of mechanical properties. UV-stabilized grades are available, but they may add to the cost.
- Lower Rigidity Compared to Some Plastics
- Flexibility:While HDPE is strong and durable, it is not as rigid as some other plastics like Polypropylene (PP) or Polyvinyl Chloride (PVC). This can limit its use in applications requiring high rigidity and stiffness.
- Difficulties in Bonding and Painting
- Surface Adhesion: HDPE’s non-polar surface makes it challenging to bond with adhesives or paint. Special surface treatments or primers are often required to improve adhesion, adding to the complexity and cost of manufacturing processes.
- Higher Shrinkage Rate
- Dimensional Stability: HDPE has a higher shrinkage rate during the cooling process, which can affect the dimensional accuracy and consistency of molded parts. This requires careful mold design and process control to ensure desired outcomes.
Applications of CNC Routers
- Packaging: Bottles, caps, and containers for food, beverages, and household products benefit from HDPE’s durability and chemical resistance.
- Automotive: Fuel tanks, bumpers, and interior components leverage HDPE’s lightweight yet robust nature.
- Construction: Pipes, fittings, and geomembranes utilize HDPE’s toughness and ability to withstand environmental stress.
- Medical: Containers, trays, and components for medical devices benefit from HDPE’s sterilizability and chemical resistance.
Conclusion
HDPE stands out as a versatile and reliable material in the world of injection molding. Its numerous advantages, including durability, chemical resistance, and cost-effectiveness, make it a preferred choice across diverse industries such as packaging, automotive, construction, and medical sectors. HDPE’s ability to be molded into complex shapes with precise dimensions further enhances its utility.
However, it is crucial to acknowledge the material’s limitations, such as susceptibility to stress cracking, poor high-temperature performance, and challenges with UV exposure. Understanding these disadvantages helps in making informed decisions about material selection and application design to ensure optimal performance.
The wide range of applications, from everyday household items to critical industrial components, underscores HDPE’s importance in modern manufacturing. With advancements in formulations and molding technologies, HDPE continues to evolve, promising even greater potential for innovative and sustainable solutions in the future.