Contents
Medical injection molding plays a crucial role in the healthcare industry, providing the means to produce complex, high-precision medical components in large quantities. This technology has revolutionized the manufacturing of medical devices, offering consistency, accuracy, and efficiency. As the demand for advanced medical equipment grows, the importance of understanding the nuances of medical injection molding becomes even more significant.
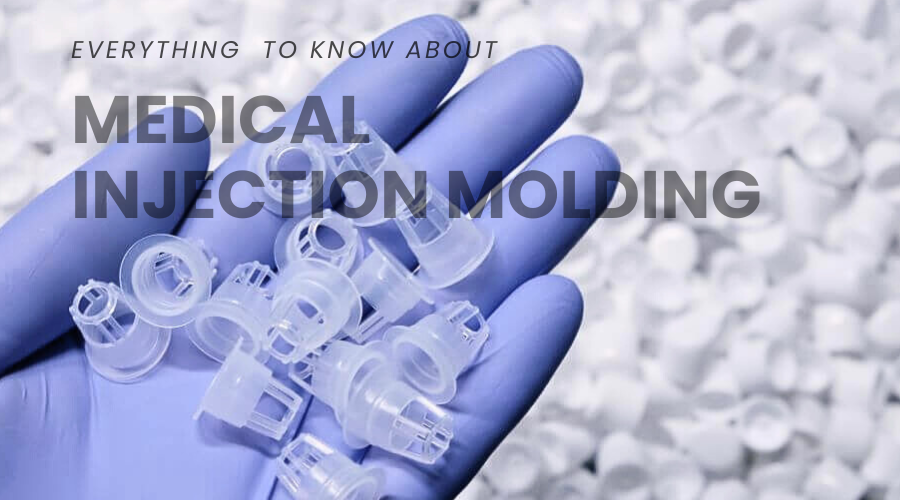
Key Requirements for Medical Device Injection Molding
The stringent requirements of the medical industry necessitate specific considerations in the injection molding process. Meeting these requirements ensures that the produced components are safe, reliable, and compliant with regulatory standards.
Material Selection
The selection of material is paramount in medical injection molding. Materials must exhibit biocompatibility, meaning they do not induce an immune response when in contact with the human body. Commonly used materials include thermoplastic like polyethylene, polypropylene, and polycarbonate, each chosen for their unique properties such as flexibility, chemical resistance, and strength. Specialty polymers like PEEK and medical-grade silicone are also used due to their high-performance characteristics in demanding medical applications. Additionally, materials must be compatible with sterilization processes like autoclaving, gamma radiation, and ethylene oxide gas sterilization to ensure the safety and sterility of medical devices.
Precision and Accuracy
Medica devices often require extrmely tihgt tolerances and consistent production to function correctly and safety. Precision in the injection molding process is achieved through meticulous mold design, advanced machinery, and rigorous process controls. This precision ensures that each component meets the exact specifications needed for its intended medical application, reducing the risk of malfunction or failure in critical situations.
Cleanroom Manufacturing
Manufacturing in a cleanroom environment is essential for medical injection molding. Cleanrooms maintain controlled levels of contamination, including dust, airborne microbes, aerosol particles, and chemical vapors. This is vital for ensuring the sterility of medical components, particularly those that come into direct contact with patients. Cleanroom calssification, such as ISO 7 or ISO 8, dictate the cleanliness level requried for different types of medical devices.
Common Materials Used
The choice of material is critical in medical plastic injection molding, as it directly impacts the performance and safety of the final product.
Thermoplastics
- Polyethylene (PE): Known for its flexibility and resistance to chemicals, PE is commonly used in applications such as tubing and disposable syringes.
- Polypropylene (PP): Valued for its strength and resistance to heat and chemicals, PP is frequently used in medical containers and lab equipment.
- Polycarbonate (PC): PC offers high strength and clarity, making it ideal for components requiring transparency, such as surgical instruments and housings for diagnostic equipment.
Specialty Polymers
- PEEK (Polyether ether ketone): This high-performance polymer is used in applications requiring exceptional mechanical properties and chemical resistance, such as in surgical implants and orthoprdic devices.
- Medical-grade silicone: Renowned for its biocompatibility and flexibility, silicone is used in products like catheters, seals, and gaskets.
Process Steps
The medical injection molding process involves serveral critical steps, each contributing to the precision and quality of the final product.
Design and Prototyping
The initial phase involves designing and prototyping the mold. Using advanced CAD (Computer-Aided Design) and CAM (Computer-Aided Manufacturing) technologies, engineers create precise mold designs tailored to the specific medical component. Prototyping allows for testing and validation of the design before full-scale prodcution, ensuring any potential issures are identified and resolved early.
Injection Molding Process
The injection molding process itself involves melting the chosen plastic material and injecting it into a mold cavity under high pressure. High precision molding techniques, such as micro-molding, allow for the prodcution of extrmely small and intricate medical components. Consistent process parameters, such as temperature, pressure, and cooling time, are crucial to maintaining tight tolerances and high0quality output.
Quality Control
Stingent quality control measures are integral to medical injection molding. Each batch of produced components undergoes rigourous testing and validation to ensure they meet all specified requirements. Quality control tests may include dimensional inspections, mechanical strength testing, biocompatibility assessments, and sterilization efficacy evaluations. These tests are essential for ensuring the safety and reliability of medical devices.
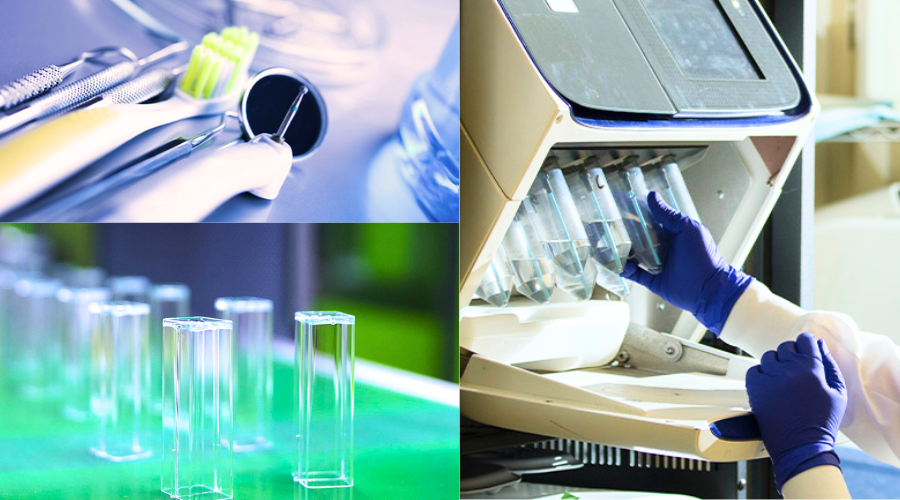
Medical Application
Medical injection molding has a wide range of applications in the healthcare industry, encompassing various types of medical devices and equipment.
Medical Devices
Injection molding is widely used in the production of medical devices such as syringes, catheters, and surgical instruments. These devices requrie high precision and must adhere to strict safety standards to ensure they function correctly and safely during medical procedures.
Diagnostic Equipment
Components for diagnostic equipment, such as housings and internal parts for MRI machines and blood analyzers, are often manufactured using injection molding. The ability to produce complex shapes with high precision is crucial for these applications, where accuracy and reliability are paramount.
Pharmaceutical Packaging
Injection molding is also employed in the production of parmaceutical packaging, including containers and closures for medications. These products must ensure the integrity and safety of phamaceutical products, preventing contamination and ensuring proper dosage.
Conlcusion
Medical injection molding is a critical technology in the healthcare indutry, enabling the production of precise, reliable, and safe medical componnets. As the demand for advanced medical equipment continues to grow, the importance of expertise in medical injection molding becomesincreasingly evident.
HordRT offers innovative solutions and state-of-the-art manufacturing capabilities in the field of medical injection molding. With a commitment to qality and regulatory compliance, HordRT is well-equipped to meet the evolving needs of the medical industry, ensuring the highest standards of safety and performance in every product.