Injection molding is a widely used manufacturing process for producing plastic parts with high precision and efficiency. One critical component of the injection molding process is the gate, which is the entry point for the molten plastic into the mold cavity. The selection of the gate type plays a significant role in determining the part quality, cycle time, and overall production costs. In this article, we will explore the various types of gates commonly used in injection molding.
Types of Injection Molding Gate
1.Sprue Gate
The sprue gate is the simplest and most commonly used gate type in injection molding. It is located at the center of the mold and serves as the entry point for the molten plastic from the injection unit. The sprue gate is connected to the runner system, which distributes the plastic to multiple cavities in multi-cavity molds. Although sprue gates leave a visible mark on the finished part, they are easy to design and provide good flow control.
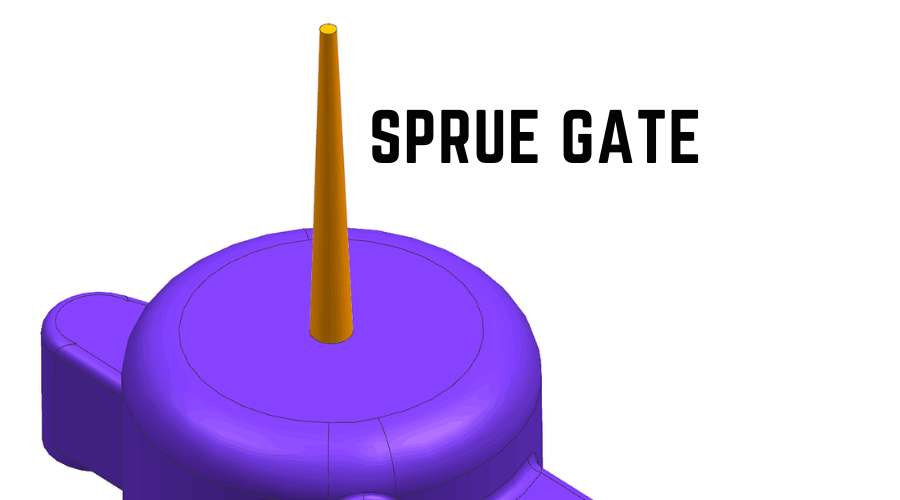
2.Submarine Gate
Submarine gates, also known as submarine or tunnel gates, are used when the appearance of the part is crucial, and gate marks should be minimized or eliminated. This type of gate is placed below the parting line, resulting in a gate mark that is concealed within the mold. Submarine gates are commonly used for cosmetic parts or components with intricate geometries.
3.Edge Gate
Edge gates, as the name suggests, are positioned at the edge of the mold cavity. They provide a direct entry point for the molten plastic, minimizing flow length and reducing the chances of undesirable flow marks on the part. Edge gates are suitable for thin-walled parts and can be advantageous when gate vestiges need to be removed easily.
4.Hot Runner Gate
Hot runner systems are used to maintain the molten plastic at a constant temperature throughout the injection molding process. The gate in a hot runner system is typically a small orifice, and it can take various forms such as pinpoint, valve, or thermal gate. Hot runner gates offer several advantages, including reduced material waste, faster cycle times, and improved control over the injection process. They are commonly used for high-volume production and complex parts.
5.Diaphragm Gate
Diaphragm gates, also known as film gates, are thin gates that are used for parts requiring a clean and consistent appearance. These gates create a thin diaphragm of plastic that seals the gate after injection, preventing any visible gate marks. Diaphragm gates are often used for optical parts, lenses, and transparent components.
6.Fan Gate
Fan gates, also called fan-shaped gates or multiple-point gates, are used when there is a need for multiple entry points for the molten plastic. These gates distribute the flow of plastic across the mold cavity, ensuring uniform filling and reducing the risk of weld lines. Fan gates are commonly used for large or complex parts where the balanced filling is critical.

7.Cashew Gate
Cashew gate, also referred to as banana gates or fan gates, are curved gates that resemble the shape of a cashew nut or a banana. These gates provide a balanced flow of plastic and are suitable for parts with complex geometries or multiple thin-walled sections. Cashew gates help prevent flow marks and improve part aesthetics.
8.Valve Gate
Valve gates, also known as needle gates or pneumatic gates, are advanced gates systems that use a mechanical valve to control the flow of plastic into the mold cavity. This gate type offers precise control over the opening and closing of the gate, resulting in reduced gate vestiges, improved part quality, and reduced scrap rates. Valve gates are commonly used for high-quality parts with strict cosmetic requirements.
Importance of Gate Location in Injection Molding
Filling Pattern and Flow Control
The gate location significantly impacts how the molten plastic flows into the mold cavity. It determines the flow path and influences the filing pattern of the part. By strategically placing the gate, manufacturers can control the flow front, minimize flow imbalances, and ensure uniform filling. Proper flow control helps prevent issues such as short shots, flow marks, or voids in the molded part.
Cooling and Warpage
The gate location affects the cooling process of the part. During the cooling phase, the molten plastic solidifies, and the part takes shape. The gate area cools differently compared to the rest of the part. Improper gate placement can result in uneven cooling, leading to internal stresses and potential warpage. By selecting an appropriate gate location, manufacturers can optimize cooling and minimize the risk of warpage or dimensional inaccuracies.
Gate Vestige and Appearance
Gate vestige refers to the visible mark or scar left on the part where the gate was located. The gate location directly influences the visibility and appearance of the gate vestige. Depending on the part’s design requirements and cosmetic considerations, manufacturers may need to place the gate in inconspicuous locations or areas where the gate vestige is easily removable or concealed. Careful gate location selection helps minimize gate vestige and improve the overall aesthetics of the molded part.
Mold Design and Complexity
The gate location also impacts mold design and complexity. It affects the runner system design, the number of cavities, and the overall mold layout. Choosing an optimal gate location can simplify mold design, reduce complexity, and enhance mold longevity. It allows for efficient material flow through the runner system and ensures balanced filling in multi-cavity molds.
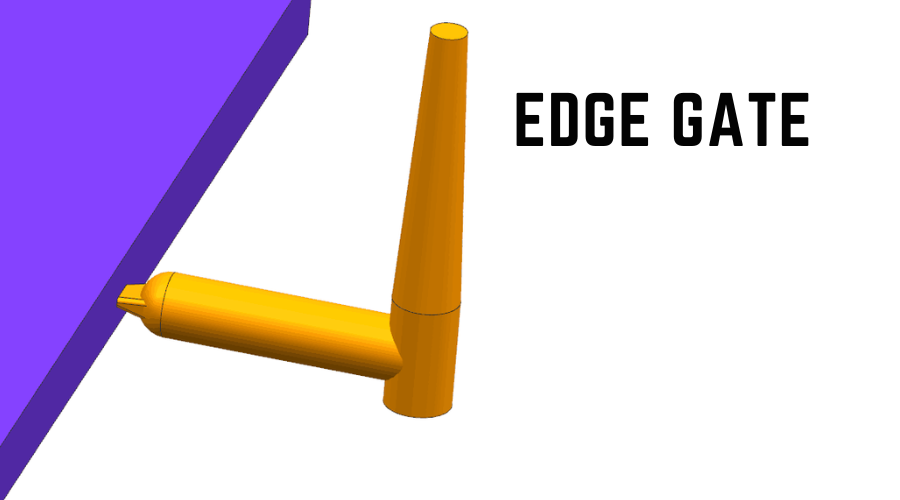
Production Efficiency and Cycle Time
Gate location can impact production efficiency and cycle time. A well-placed gate facilitates faster filling and better packing of the molten plastic, reducing cycle times. It also allows for easy gate removal or trimming, streamlining post-processing operations.
Conclusion
In conclusion, the selection of the gate type in injection molding is a critical aspect of the manufacturing process. Different types of gates offer distinct advantages and considerations, depending on factors such as part design, materials properties, cosmetic requirements, and production volume.
Understanding the characteristics and applications of different gate types empowers manufacturers to make informed decisions, leading to improved part aesthetics, reduced production costs, and enhanced overall customer satisfaction. As injection molding continues to evolve, the gate selection process will process will remain a crucial factor in achieving successful and efficient plastic part production.